Back
Production Part Approval Process (PPAP)
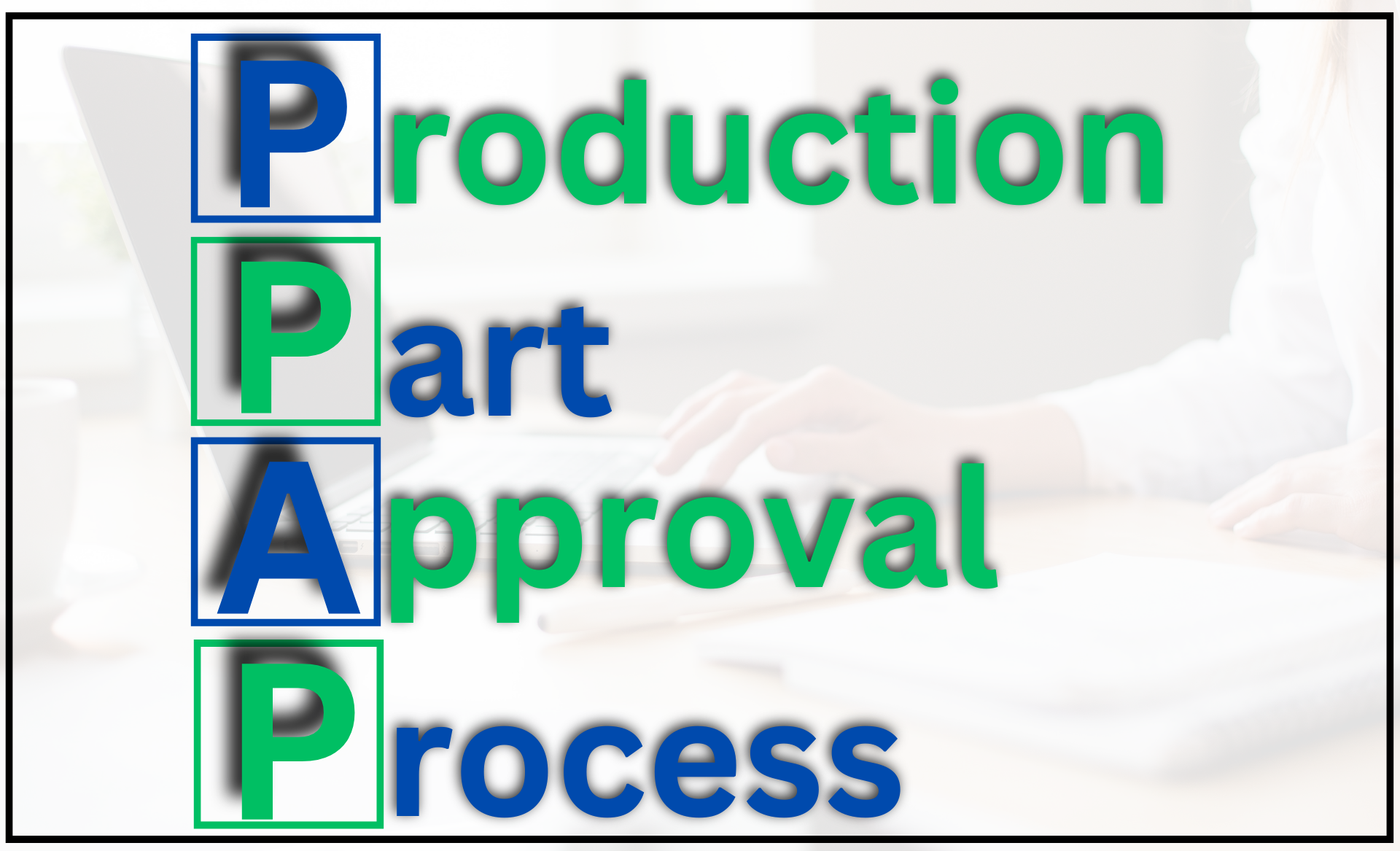
Production Part Approval Process
- What is PPAP?
- When to Perform PPAP?
- How to Perform PPAP?
- What are the benefits of PPAP?
- What's the difference between PPAP and APQP?
- Why Perform PPAP?
Introduction to PPAP :-
In a world fueled by constant evolution and dynamic change, the pursuit of perfection is a perpetual journey. As industries traverse the ever-shifting landscapes of technology, manufacturing, and innovation, the need for robust quality management systems becomes paramount. Enter the stage, the Production Part Approval Process (PPAP), a symphony of meticulous protocols and rigorous standards orchestrating the seamless integration of innovation and reliability.
PPAP isn't merely an acronym; it's the conductor of a carefully choreographed performance that ensures every part and process harmonizes flawlessly within the grand composition of production. Originating from the automotive industry, PPAP has transcended its roots to become a universal language spoken by diverse sectors aiming to deliver excellence in their creations.
This introduction embarks on a journey to unravel the layers of PPAP, delving into its significance in today's fast-paced industrial panorama. Join us as we explore how PPAP transcends the conventional, transforming into a dynamic force that propels industries toward unparalleled efficiency, consistency, and quality. It's not just a protocol; it's a testament to the commitment to precision, a testament that resonates across sectors where innovation and reliability converge. Welcome to the world where PPAP takes center stage, transforming challenges into opportunities and setting the rhythm for the future of manufacturing excellence.
What is PPAP :-
PPAP stands for Production Part Approval Process. It is a standardized approach in the automotive and other manufacturing industries to ensure that a supplier's components or materials meet the required specifications and will consistently yield products of high quality.
The PPAP process involves a series of documentation and validation steps that a supplier must go through before their parts are incorporated into the production process. This helps to verify that the supplier can consistently meet the customer's requirements and specifications. The primary goal of PPAP is to prevent defects in the early stages of the product development cycle, ensuring that potential issues are identified and addressed before mass production.
Key components of the PPAP process typically include:
- Design Records: Documentation of the design process and specifications.
- Engineering Change Documents: Any changes made to the product design.
- Process Flow Diagrams: Illustrations of the manufacturing process.
- Process Failure Mode and Effects Analysis (PFMEA): Identification and analysis of potential failure modes.
- Control Plan: Outlining the steps and measures in the manufacturing process to ensure consistency.
- Measurement System Analysis (MSA): Ensuring that measurement systems are accurate and reliable.
- Dimensional Results: Actual measurements of key product characteristics.
- Initial Sample Inspection Report (ISIR): Inspection and validation of the initial product samples.
What are the benefits of PPAP? :-
The Production Part Approval Process (PPAP) offers several benefits to both suppliers and customers in the manufacturing industry. Here are some key advantages:
- Quality Assurance: PPAP ensures that the production process consistently meets the specified requirements. By thoroughly validating and documenting each step of the manufacturing process, the likelihood of defects is significantly reduced, leading to higher overall product quality.
- Early Identification of Issues: Through the comprehensive documentation and validation process, potential issues and defects are identified early in the product development cycle. This early detection allows for timely adjustments and corrections, preventing the need for costly rework or production delays.
- Risk Mitigation: PPAP includes tools such as Process Failure Mode and Effects Analysis (PFMEA), which helps identify and prioritize potential failure modes in the manufacturing process. This proactive approach allows organizations to mitigate risks before they impact production.
- Supplier-Customer Collaboration: PPAP fosters a collaborative relationship between suppliers and customers. By clearly defining expectations, specifications, and quality standards, both parties can work together to ensure that the final product meets or exceeds the required quality levels.
- Consistency in Production: The detailed documentation and control plans in PPAP contribute to consistent and repeatable manufacturing processes. This consistency is essential for meeting customer expectations and maintaining a positive reputation in the market.
- Compliance with Industry Standards: PPAP is often a requirement in industries with stringent quality standards, such as automotive manufacturing. Adhering to PPAP guidelines helps organizations demonstrate compliance with industry-specific standards and regulations.
- Efficient Change Management: When changes are made to the product design or manufacturing process, the PPAP process ensures that these changes are thoroughly documented, reviewed, and approved. This helps prevent unintended consequences and ensures that all parties involved are aware of and prepared for the modifications.
- Customer Confidence: Customers gain confidence in the reliability of the supplied products when they see that a supplier has completed the PPAP process. This confidence can lead to stronger and more long-term business relationships.
- Cost Savings: While the initial implementation of PPAP may involve additional efforts and resources, the long-term benefits include cost savings due to reduced defects, rework, and warranty claims. It contributes to overall operational efficiency and cost-effectiveness.
In summary, PPAP is a systematic and structured approach that brings about improved quality, reduced risks, and enhanced collaboration between suppliers and customers in the manufacturing industry.
How to Perform PPAP :-
Performing a Production Part Approval Process (PPAP) involves a series of well-defined steps and documentation to ensure that the manufacturing process consistently meets customer requirements. Here's a general guide on how to perform PPAP:
1. Understand Customer Requirements:
- Review and understand the customer's specifications and expectations for the product.
2. Create a Cross-Functional Team:
- Assemble a team that includes representatives from various departments such as design, production, quality, and engineering.
3. Document Product and Process Information:
- Gather and document information related to product design, manufacturing processes, and materials used.
4. Complete Design Records:
- Document the design process, including engineering drawings, specifications, and any changes made during the design phase.
5. Conduct a Risk Assessment (PFMEA):
- Perform a Process Failure Mode and Effects Analysis (PFMEA) to identify and prioritize potential failure modes in the manufacturing process.
6. Develop a Control Plan:
- Create a Control Plan that outlines the key steps in the manufacturing process and specifies how each step will be controlled to ensure quality.
7. Implement the Manufacturing Process:
- Start the production of the initial samples using the documented manufacturing process.
8. Collect and Analyze Data:
- Collect data on critical product characteristics during the manufacturing process and conduct a Measurement System Analysis (MSA) to ensure accurate measurements.
9. Create an Initial Sample Inspection Report (ISIR):
- Prepare an Initial Sample Inspection Report, including measurements, inspection results, and any non-conformance issues identified.
10. Submit PPAP Package to Customer:
- Compile all relevant documentation, including design records, PFMEA, control plan, ISIR, and other required forms into a comprehensive PPAP package.
11. Customer Review and Approval:
- Submit the PPAP package to the customer for review. The customer evaluates the documentation and may conduct on-site audits or inspections.
12. Address Customer Feedback:
- Address any feedback or concerns raised by the customer. Make necessary adjustments to the manufacturing process or documentation.
13. Final Approval and Production:
- Once the customer is satisfied, obtain final approval to start full-scale production.
14. Maintain Records:
- Keep thorough records of the PPAP process, including any changes made during production, and update documentation as needed.
15. Continuous Improvement:
- Implement continuous improvement processes to enhance product quality and efficiency over time.
Tips:
- Follow the PPAP manual or guidelines provided by the customer or industry standards (e.g., AIAG PPAP Manual in the automotive industry).
- Communicate effectively with the customer throughout the PPAP process.
- Ensure that all team members are trained in PPAP requirements and procedures.
Remember that specific industry requirements may vary, so it's crucial to consult the relevant standards and guidelines applicable to your industry.
What's the difference between PPAP and APQP? :-
PPAP (Production Part Approval Process) and APQP (Advanced Product Quality Planning) are both important components of quality management systems in the manufacturing industry, particularly in sectors like automotive. While they are distinct processes, they are closely related and often used in conjunction. Here are the key differences between PPAP and APQP:
1. Purpose:
- PPAP (Production Part Approval Process): Primarily focused on providing evidence that a supplier's production process can consistently produce parts meeting the customer's requirements during actual production.
- APQP (Advanced Product Quality Planning): Geared toward the planning and development phases of a new product or process, ensuring that quality is built into the product from the early design stages.
2. Timing in the Product Lifecycle:
- PPAP: Typically conducted after the production process has been established and parts have been manufactured. It is the final step before mass production begins.
- APQP: Implemented during the initial stages of product development, including the planning, design, and prototyping phases.
3. Focus on Production vs. Planning:
- PPAP: Emphasizes the actual production process and aims to demonstrate that the process is capable of consistently producing parts meeting specified requirements.
- APQP: Concentrates on planning and preventing issues before they occur by proactively considering and addressing potential risks in the design and manufacturing processes.
4. Documentation:
- PPAP: Involves the submission of a comprehensive documentation package, including process documentation, inspection results, and other relevant records, to demonstrate the capability of the production process.
- APQP: Requires the creation of a detailed plan outlining the steps to be taken during the product development process to ensure that quality is built into the product.
5. When They Occur in the Product Lifecycle:
- PPAP: Usually performed for existing products or processes before significant changes are made or when a new part is introduced.
- APQP: Conducted for new product launches or major changes to existing products.
6. Customer Involvement:
- PPAP: Involves submitting documentation to the customer for review and approval but is more focused on the supplier's processes.
- APQP: Encourages close collaboration between suppliers and customers during the planning stages to align on quality expectations and prevent issues.
7. Standards and Guidelines:
- PPAP: Guidelines are often outlined in industry-specific standards like the AIAG PPAP manual.
- APQP: Guidelines are typically specified in industry standards such as the AIAG APQP manual.
In summary, while PPAP and APQP serve different purposes in the product development and production processes, they are interconnected components of a robust quality management system. APQP lays the groundwork for quality in the planning stages, and PPAP ensures that the established processes can consistently meet quality requirements during actual production. Both processes contribute to the overall goal of delivering high-quality products to customers.
Why Perform PPAP : -
Performing the Production Part Approval Process (PPAP) is crucial for several reasons, all of which contribute to ensuring the quality, consistency, and reliability of products in manufacturing industries. Here are some key reasons why PPAP is performed:
- Quality Assurance : PPAP is a systematic approach to verifying that the manufacturing process can consistently produce parts that meet the specified requirements. It helps ensure that the product is of high quality, minimizing the risk of defects.
- Risk Mitigation: Through tools like Process Failure Mode and Effects Analysis (PFMEA), PPAP allows for the identification and prioritization of potential failure modes in the manufacturing process. This proactive approach helps in mitigating risks before they lead to production issues.
- Customer Satisfaction: PPAP provides a structured framework for communication and collaboration between suppliers and customers. By demonstrating a commitment to quality and providing evidence of process capability, suppliers can instill confidence in their customers.
- Regulatory Compliance: In industries with stringent quality standards and regulations, such as automotive manufacturing, PPAP is often a requirement for compliance. Meeting PPAP guidelines ensures that products adhere to industry-specific standards.
- Early Issue Detection: PPAP is conducted before full-scale production begins, allowing for the early detection of issues and defects. This early identification enables corrective actions to be implemented before large quantities of non-conforming products are produced.
- Efficient Change Management: When changes are made to the product design or manufacturing process, PPAP ensures that these changes are thoroughly documented, reviewed, and approved. This helps prevent unintended consequences and ensures that all parties involved are aware of and prepared for modifications.
- Continuous Improvement: PPAP encourages a culture of continuous improvement. By documenting and analyzing the results of the initial production run, organizations can identify areas for improvement in processes and make adjustments to enhance efficiency and quality.
- Supplier-Customer Collaboration: PPAP fosters a collaborative relationship between suppliers and customers. It provides a transparent view of the production process, allowing both parties to work together to address challenges and optimize the manufacturing process.
- Cost Savings: While there are initial costs associated with implementing PPAP, the long-term benefits include cost savings due to reduced defects, rework, and warranty claims. It contributes to overall operational efficiency and cost-effectiveness.
- Competitive Advantage: Organizations that consistently demonstrate their ability to meet and exceed quality standards through PPAP gain a competitive advantage. Customers often prefer suppliers with established and validated production processes.
In summary, performing PPAP is essential for maintaining and enhancing product quality, meeting regulatory requirements, and building strong relationships with customers. It is a proactive approach to quality management that contributes to the long-term success of manufacturing organizations.