Back
Understanding APQP and PPAP: Your Guide to Quality Assurance in Automotive Manufacturing
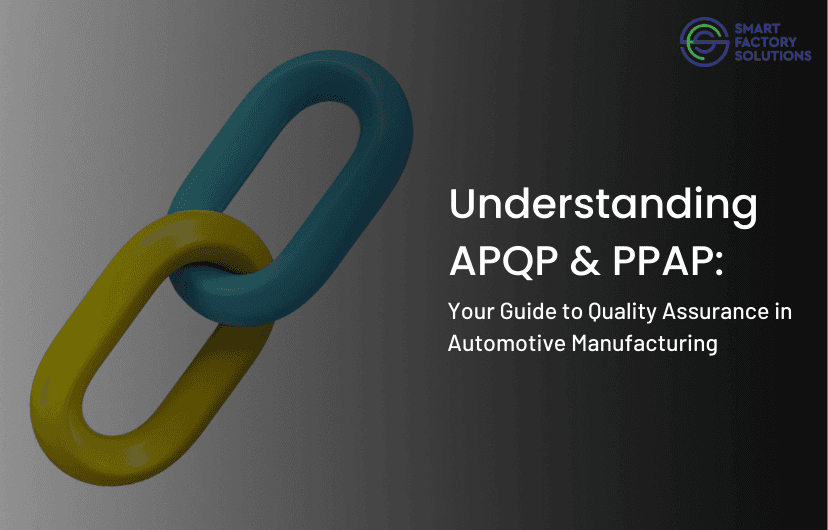
In the world of automotive manufacturing, ensuring the highest quality of products is paramount. This goal is achieved through a variety of standardized processes, two of the most critical being Advanced Product Quality Planning (APQP) and Production Part Approval Process (PPAP). Both frameworks are designed to ensure that automotive parts and components meet the rigorous quality standards required in the industry. This guide will delve into the intricacies of APQP and PPAP, providing a comprehensive understanding of their roles, processes, and benefits in quality assurance.
What is APQP?
Advanced Product Quality Planning (APQP) is a systematic method for developing and designing products and processes. Ensure that the final product meets customer requirements and expectations. This methodology is divided into five phases:
1. Plan and Define Program: This phase involves understanding customer needs and expectations. It includes defining the project scope, goals, and deliverables. Key activities include creating a product quality plan, conducting feasibility studies, and identifying critical design and process characteristics.
2. Product Design and Development: This phase focuses on designing the product. It involves creating design specifications, conducting design reviews, and developing prototypes. Tools such as Failure Mode and Effects Analysis (FMEA) and Design for Manufacturability and Assembly (DFMA) are commonly used.
3. Process Design and Development: This is where the manufacturing process is designed. This includes developing process flow charts, conducting process FMEA, and creating control plans. The goal is to establish a robust manufacturing process that consistently produces high-quality products.
4. Product and Process Validation: This phase involves validating the product and process through production trials. It includes conducting capability studies, pilot production runs, and initial sample inspections. The aim is to ensure that the product meets all specifications and is ready for mass production.
5. Feedback, Assessment, and Corrective Action: The final phase focuses on continuous improvement. It involves gathering feedback from customers, assessing process performance, and implementing corrective actions as needed. The objective is to maintain and improve product quality over time.
In-Depth Look at APQP Phases
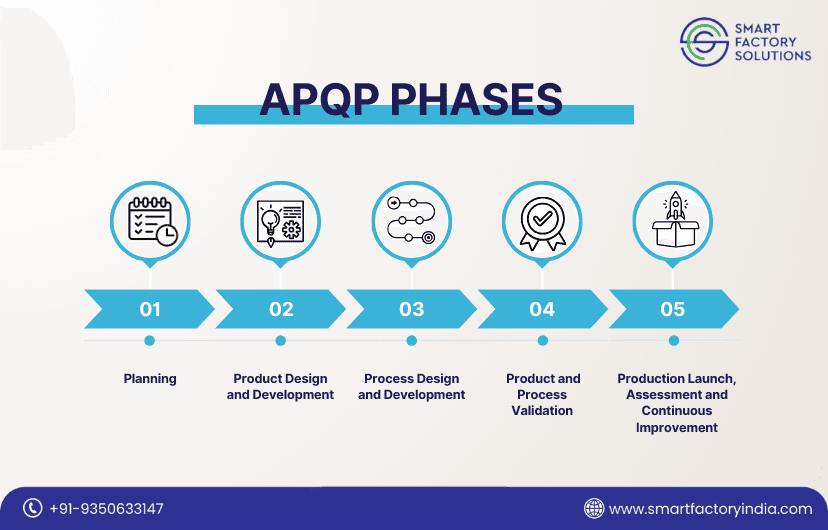
1. Plan and Define Program: The initial phase of APQP focuses on understanding and defining the requirements of the customer. This involves detailed discussions with the customer to understand their needs, expectations, and specifications. Creating a product quality plan is crucial at this stage. This plan outlines the project's scope, goals, and deliverables. A feasibility study is conducted to assess whether the project can be completed within the given constraints. Identifying critical design and process characteristics is essential to ensure that the final product meets the desired quality standards.
2. Product Design and Development: In the product design and development phase, the focus shifts to creating a detailed design of the product. This includes developing design specifications, conducting design reviews, and building prototypes. Tools such as Failure Mode and Effects Analysis (FMEA) are used to identify potential failure modes in the design phase and take corrective actions to mitigate them. Design for Manufacturability and Assembly (DFMA) is another important tool used to ensure that the product design is optimized for efficient manufacturing and assembly processes.
3. Process Design and Development: The process design and development phase involve designing the manufacturing process for the product. This includes developing process flow charts that outline each step of the manufacturing process. Conducting process FMEA helps identify potential failure modes in the manufacturing process and take corrective actions to mitigate them. Creating control plans is essential to ensure that the manufacturing process consistently produces high-quality products. Control plans outline the methods and measures that will be used to monitor and control the manufacturing process.
4. Product and Process Validation: In the product and process validation phase, the product and manufacturing process are validated through production trials. This includes conducting capability studies to assess the ability of the manufacturing process to produce products that meet specifications. Pilot production runs are conducted to identify and address any issues before full-scale production begins. Initial sample inspections are performed to ensure that the product meets all specifications and requirements.
5. Feedback, Assessment, and Corrective Action: The final phase of APQP focuses on continuous improvement. This involves gathering feedback from customers, assessing the performance of the manufacturing process, and implementing corrective actions as needed. The objective is to maintain and improve product quality over time. Continuous improvement is a key principle of APQP and is essential to ensure that the product and manufacturing process continues to meet customer requirements and expectations.
Benefits of APQP
- Improved Quality: APQP ensures that quality is built into the product from the initial design phase, leading to higher-quality final products.
- Cost Savings: By identifying potential issues early in the development process, APQP helps reduce the cost of rework and scrap.
- Customer Satisfaction: Meeting customer requirements and expectations leads to higher levels of customer satisfaction.
- Efficiency: A structured approach to product development helps streamline processes and reduce development time.
- Risk Management: Identifying potential risks and mitigating them early in the process helps minimize the likelihood of quality issues.
- Regulatory Compliance: Adhering to APQP standards helps ensure compliance with industry regulations and standards.
What is PPAP?
Production Part Approval Process (PPAP) is a standardized process in the automotive industry that helps ensure that the supplier's production process can consistently produce parts that meet customer requirements. PPAP is a critical component of the APQP process and is typically required for any new or significantly modified part.
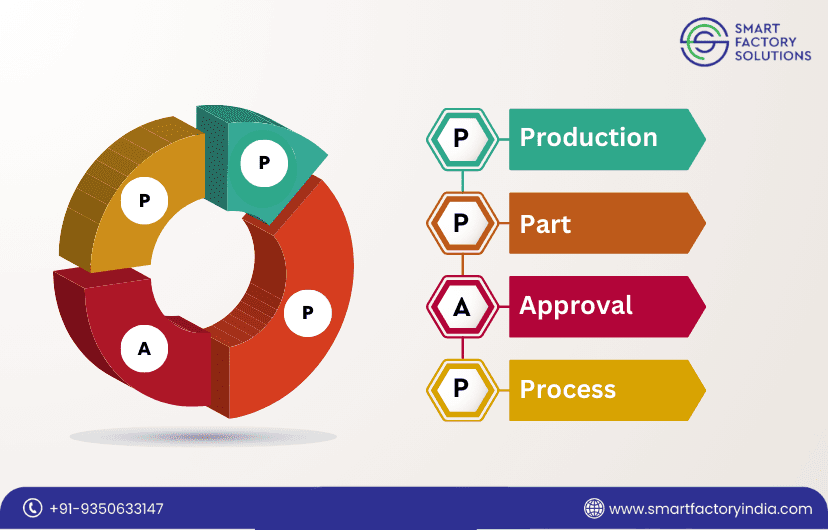
In-Depth Look at PPAP Elements
1. Design Records: Design records include detailed drawings and specifications of the part. These records are essential to ensure that the part is manufactured according to the specified design. Any changes made to the design must be documented and approved by the customer.
2. Engineering Change Documents: Engineering change documents record any changes made to the design. These documents are important to ensure that all changes are properly reviewed and approved by the customer. This helps maintain the integrity of the design and ensures that the final product meets customer requirements.
3. Customer Engineering Approval: Customer engineering approval is evidence that the customer has approved the design. This approval is essential to ensure that the design meets the customer's requirements and expectations. With customer approval, the part can proceed to production.
4. Design FMEA: Design FMEA is an analysis of potential failure modes in the design phase. This analysis helps identify and mitigate potential risks early in the design process. By addressing potential failure modes early, the likelihood of quality issues in the final product is reduced.
5. Process Flow Diagram: The process flow diagram is a visual representation of the manufacturing process. It outlines each step and helps identify potential areas for improvement. By understanding the flow of the process, potential bottlenecks and inefficiencies can be addressed.
6. Process FMEA: Process FMEA is an analysis of potential failure modes in the manufacturing process. This analysis helps identify and mitigate potential risks in the production process. By addressing potential failure modes early, the likelihood of quality issues in the final product is reduced.
7. Control Plan: The control plan is a detailed plan for controlling the manufacturing process. This plan outlines the methods and measures that will be used to monitor and control the process. By following the control plan, the manufacturing process can consistently produce high-quality products.
8. Measurement System Analysis: Measurement system analysis evaluates the measurement systems used in the process. This analysis ensures that the measurement systems are accurate and reliable, which is essential to ensuring that the parts meet specifications.
9. Dimensional Results: Dimensional results include measurements of the part to ensure it meets specifications. These measurements are essential to verify that the part is manufactured according to the design. Any deviations from the specifications must be addressed before the part can proceed to production.
10. Material/Performance Test Results: Material and performance test results provide evidence that the part meets all material and performance requirements. These tests are essential to ensure that the part performs as expected in its intended application. Any issues identified during testing must be addressed before the part can proceed to production.
11. Initial Process Studies: Initial process studies assess the manufacturing process's ability to produce parts that meet specifications. These studies include capability studies and pilot production runs to identify and address any issues before full-scale production begins.
12. Qualified Laboratory Documentation: Qualified laboratory documentation provides certification of any laboratories used for testing. This ensures that the laboratories meet industry standards and that the test results are reliable and accurate.
13. Appearance Approval Report: The appearance approval report is the customer's approval of the part's appearance. This approval is essential to ensure that the part meets the customer's aesthetic requirements and expectations.
14. Sample Production Parts: Sample production parts are samples provided to the customer for approval. These samples are used to verify that the parts meet all specifications and requirements.
15. Master Sample: A master sample is a part kept for reference. It is used as a benchmark to ensure that future production parts meet the same specifications and quality standards.
16. Checking Aids: Checking aids include tools and fixtures used to check the part during production. These aids are essential to ensure that the parts are manufactured according to the specifications.
17. Customer-Specific Requirements: Customer-specific requirements include any additional requirements specified by the customer. These requirements must be met in addition to the standard PPAP requirements.
18. Part Submission Warrant (PSW): The part submission warrant is formal documentation that the part meets all customer requirements and specifications. The supplier signs this warrant and submits it to the customer for approval.
Differences Between APQP and PPAP
While APQP and PPAP are closely related and often used together, they serve different purposes in the quality assurance process. Here are some key differences:
1. Scope and Purpose:
- APQP: APQP is a broader framework that covers the entire product development process, from planning and design to production and continuous improvement. It is focused on ensuring that the product meets customer requirements and is developed efficiently and effectively.
- PPAP: PPAP is a more specific process focused on ensuring that the supplier's production process consistently produces parts that meet customer requirements. It is typically used for new or significantly modified parts.
2. Phases and Elements:
- APQP: APQP consists of five phases that cover the entire product development lifecycle, including planning, product design, process design, validation, and continuous improvement.
- PPAP: PPAP consists of 18 elements that provide detailed documentation and evidence that the production process can consistently produce parts that meet specifications.
3. Timing:
- APQP: APQP is used throughout the entire product development process, from the initial planning phase to the final production and continuous improvement phases.
- PPAP: PPAP is typically used at a specific point in the product development process, usually when a new or significantly modified part is being introduced into production.
4. Focus:
- APQP: APQP has a broader focus that includes product design, process design, and continuous improvement. It is focused on ensuring that the entire product development process is efficient and effective.
- PPAP: PPAP has a narrower focus, specifically on the production process. It is focused on ensuring that the process consistently produces parts that meet specifications.
5. Output:
- APQP: The output of APQP is a comprehensive quality plan that covers the entire product development process and ensures that the product meets customer requirements.
- PPAP: The output of PPAP is a set of documents and evidence that demonstrate that the production process can consistently produce parts that meet specifications.
Conclusion
APQP and PPAP are essential frameworks in the automotive manufacturing industry that help ensure the highest quality of products. APQP provides a structured approach to product and process design, covering the entire product development lifecycle from planning to continuous improvement. PPAP, on the other hand, is a more specific process that ensures that the supplier's production process can consistently produce parts that meet customer requirements.
By understanding and implementing APQP and PPAP, manufacturers can improve product quality, reduce costs, increase customer satisfaction, and ensure compliance with industry standards and regulations. These frameworks provide a systematic approach to quality assurance that helps identify and mitigate potential risks early in the development process, leading to higher-quality final products.
In summary, APQP and PPAP are complementary processes that work together to ensure that automotive parts and components meet the industry's rigorous quality standards. By leveraging these frameworks, manufacturers can achieve their goal of producing high-quality products that meet customer requirements and expectations.