Back
Choosing between APQP Software and Traditional APQP Methods: A Guide for Automotive Companies
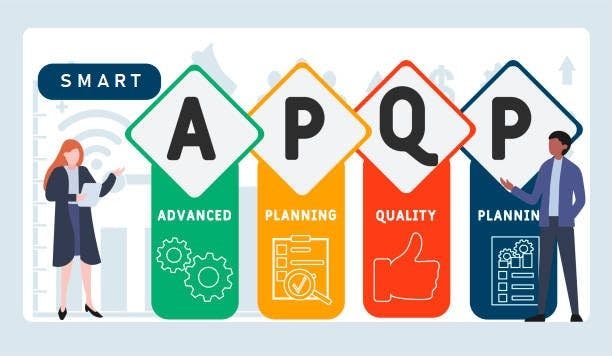
As the automotive industry continues to evolve, companies must adapt to meet changing customer demands and regulations. This requires an effective and efficient new product development (NPD) process that ensures quality, reliability, and compliance. One key aspect of this process is Advanced Product Quality Planning (APQP), which helps companies plan, design, and manufacture products that meet customer expectations.
Traditionally, companies have used manual or spreadsheet-based methods for APQP, which can be time-consuming, error-prone, and difficult to manage. However, with the advent of APQP software, companies now have access to powerful tools that can streamline and automate their APQP process, resulting in better collaboration, data accuracy, and compliance.
So, which approach is right for your company? Let's take a closer look at the pros and cons of APQP software and traditional APQP methods:
APQP Software:
Pros:
- Streamlines and automates the APQP process, reducing errors and increasing efficiency
- Provides a platform for collaboration, data sharing, and project management
- Offers real-time visibility into project progress and status, allowing for better decision-making
- Enables easier compliance with industry regulations and customer requirements
- Can be customized to suit the specific needs of your company
Cons:
- May require a significant upfront investment in software, hardware, and training
- May require IT support for implementation and maintenance
- May require some adjustment to existing workflows and processes
Traditional APQP Methods:
Pros:
- May be more familiar and comfortable for employees who are used to manual or spreadsheet-based methods
- Highly flexible allow users to copy paste and modify information as per requirement.
- May require less upfront investment in software and hardware
Cons:
- Can be time-consuming, error-prone, and difficult to manage
- Are less secure, as sensitive data is stored on individual computers or servers
- May not provide real-time visibility into project progress and status, making it harder to make informed decisions
- May not be as effective at ensuring compliance with industry regulations and customer requirements
Ultimately, the choice between APQP software and traditional APQP methods depends on your company's unique needs, resources, and goals. Some key considerations are
- Your company is engaged in multiple NPD projects
- You have a team of more than 5 people
- On-time performance
- Accuracy of documentation and process adherence.
- Security and availability of current and historical data.
The key to choosing the right approach is to carefully evaluate your company's needs and objectives, and to choose a solution that aligns with them. By choosing the right APQP approach, automotive suppliers and OEMs can improve their NPD process, reduce costs, and deliver high-quality products that meet customer expectations.
If you're still unsure whether traditional APQP methods or APQP software is the right choice for your company, our team at SFS can help. We specialize in providing APQP software solutions tailored to the needs of automotive manufacturers in India. Contact us today to schedule a consultation and learn how we can help you streamline your NPD process and achieve better outcomes.