Back
How to Find a Critical Element of a Manufacturing Process Using FMEA
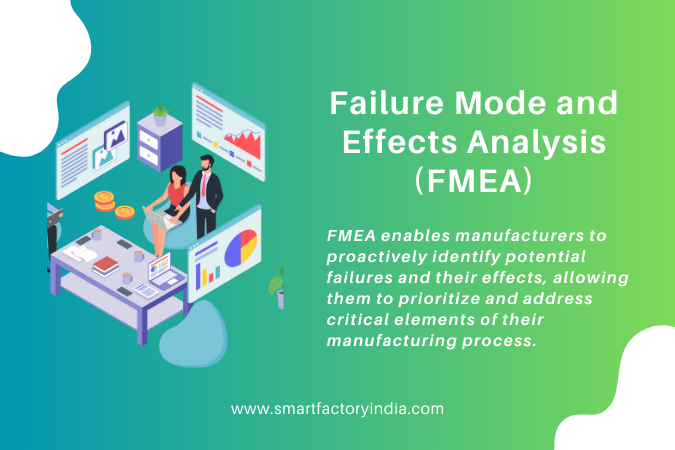
In the world of manufacturing, ensuring the highest level of product quality is essential for success. To achieve this, companies employ various methodologies and tools to identify and mitigate risks throughout the production process. One powerful tool that plays a pivotal role in risk management is Failure Mode and Effects Analysis (FMEA). FMEA enables manufacturers to proactively identify potential failures and their effects, allowing them to prioritize and address critical elements of their manufacturing process.
So, how can you effectively utilize FMEA to find the critical elements of your manufacturing process? Let's dive into the key steps:
- Assemble a Cross-Functional Team: Start by bringing together a diverse team comprising individuals from different departments, such as engineering, production, quality assurance, and operations. This collaborative approach ensures a comprehensive understanding of the manufacturing process from various perspectives.
- Define the Scope: Clearly define the scope of your FMEA analysis. Identify the specific manufacturing process or sub-process that you want to evaluate. By narrowing down the focus, you can allocate sufficient time and resources to thoroughly analyze the critical elements.
- Break Down the Process: Break down the selected manufacturing process into manageable steps or components. This step-by-step approach allows for a more detailed analysis and identification of potential failure modes.
- Identify Potential Failure Modes: For each process step, brainstorm and identify potential failure modes. These are the ways in which the process can fail or deviate from its intended functionality. Consider factors such as equipment malfunctions, material defects, human errors, or environmental factors that could impact the process.
- Evaluate Severity, Occurrence, and Detection: Assign a numerical rating to each failure mode based on its severity (impact on the final product or customer), occurrence (likelihood of the failure mode occurring), and detection (ability to detect the failure mode before it reaches the customer). This evaluation helps prioritize the critical elements that require immediate attention.
- Calculate Risk Priority Number (RPN): Multiply the severity, occurrence, and detection ratings to calculate the Risk Priority Number (RPN) for each failure mode. The higher the RPN, the more critical the element is in the manufacturing process. Focus on the failure modes with the highest RPNs as they pose the greatest risk.
- Implement Mitigation Strategies: Once you have identified the critical elements, develop and implement mitigation strategies to address and minimize the risks associated with those elements. This could involve process modifications, additional quality control measures, training programs, or equipment upgrades.
- Monitor and Review: Regularly monitor and review the effectiveness of the implemented mitigation strategies. As your manufacturing process evolves, new risks may arise or existing risks may change. Stay vigilant and adjust your strategies accordingly to ensure continuous improvement.
By following these steps, you can leverage the power of FMEA to identify and address critical elements within your manufacturing process. The proactive approach enabled by FMEA helps reduce the likelihood of failures, enhances product quality, and increases customer satisfaction.
Remember, FMEA is an ongoing process. As you gain experience and gather data, refine your analysis and incorporate feedback from your team and stakeholders. By continuously improving your FMEA practices, you can create a robust and resilient manufacturing process that consistently delivers high-quality products.
If you're looking to streamline your FMEA and risk management processes, consider utilizing advanced software solutions like SFS’s APQP Software. Our software provides a user-friendly interface, automated calculations, and real-time collaboration features to enhance the effectiveness of your FMEA analysis. Contact us today to learn more about how our software can empower your manufacturing process and drive continuous improvement.