Back
PPAP Checklists in APQP: Ensuring Compliance and Streamlining the Approval Process
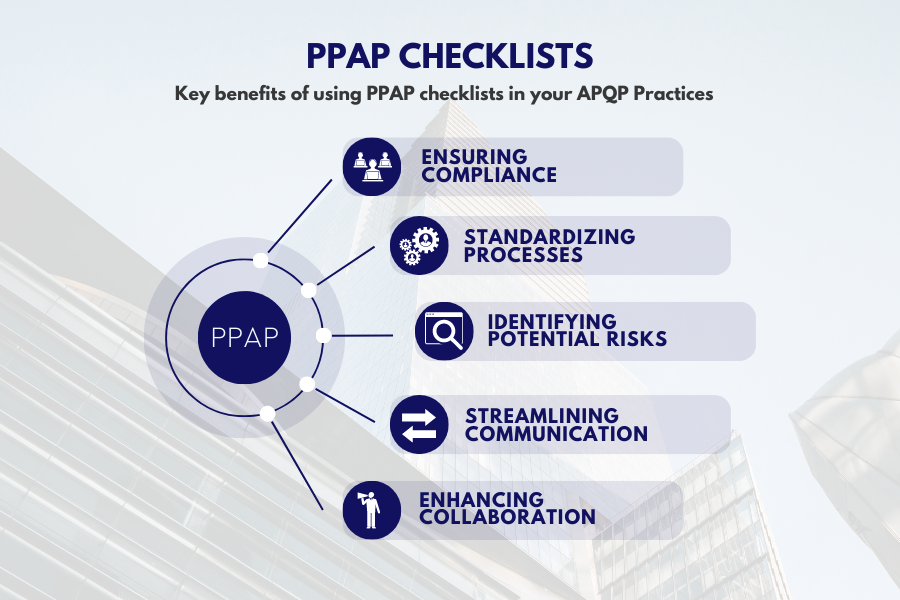
As a manufacturer, ensuring the quality and reliability of your products is of utmost importance. The Production Part Approval Process (PPAP) plays a crucial role in achieving this goal. It is a comprehensive set of guidelines and requirements that ensures the components and parts you receive from suppliers meet the necessary specifications and standards.
To simplify and streamline the PPAP process, many companies rely on PPAP checklists within the Advanced Product Quality Planning (APQP) framework. These checklists serve as a systematic approach to ensure compliance and thoroughness throughout the approval process.
Here are the key benefits of using PPAP checklists in your APQP practices:
- Ensuring Compliance: PPAP checklists act as a comprehensive tool to verify that all necessary documentation, such as engineering drawings, specifications, and test results, are in place. They help you ensure compliance with customer-specific requirements, industry standards, and regulatory guidelines.
- Standardizing Processes: PPAP checklists provide a standardized approach to gathering and organizing relevant information for each component or part. By following a consistent checklist, you can eliminate variations and maintain uniformity in the approval process.
- Identifying Potential Risks: PPAP checklists prompt you to conduct a thorough assessment of potential risks associated with the components or parts. By identifying these risks early on, you can take proactive measures to mitigate them, resulting in improved product quality and reliability.
- Streamlining Communication: PPAP checklists facilitate effective communication between your organization and suppliers. By clearly outlining the required information and documentation, you can streamline the exchange of data, reducing delays and ensuring a smooth approval process.
- Enhancing Collaboration: PPAP checklists encourage collaboration between cross-functional teams involved in the APQP process. By having a shared checklist, everyone can contribute their expertise and ensure that all necessary elements are addressed, fostering a culture of collaboration and accountability.
To leverage the benefits of PPAP checklists effectively, consider using digital tools or software solutions that automate the checklist creation and tracking process. These tools can help you streamline data collection, documentation, and collaboration, reducing manual effort and enhancing overall efficiency.
In conclusion, utilizing PPAP checklists within the APQP framework is essential for ensuring compliance, streamlining the approval process, and achieving product quality excellence. By following a structured approach, you can enhance collaboration, mitigate risks, and maintaina high level of confidence in the components and parts you incorporate into your products.
Remember, effective use of PPAP checklists requires continuous improvement and adaptability to changing industry requirements. Stay updated with the latest standards, regulations, and customer-specific requirements to ensure your PPAP practices remain robust and effective.
At Smart Factory Solutions, we understand the importance of successful PPAP implementation. Our APQP software includes measures to ensure seamless PPAP compliance and stays up to date with the latest standards and regulations. Contact us today to learn more about how our software can support your PPAP and APQP processes.